Ingot of solar-grade silicon. Photo: Elkem Solar
1 Apr 2009
Solar silicon production takes off in Norway
In late 2008 – early 2009, Norwegian Orkla-owned Elkem Solar AS completed a new metallurgical plant for smelting silicon and tested its innovative production line in Kristiansand, southern Norway. The project has been partly financed with a loan from NIB totalling EUR 145 million.
The Elkem Solar plant is a result of 25 years of research and development of a viable metallurgical production process for solar-grade silicon.
“Our aim is to industrialise a process that will result in lower costs and is better suited to producing large volumes than other, more traditional technologies in the industry,” says Helge Aasen, Senior Vice President, Business Unit, at Elkem Solar.
Solid competence
As one of the world’s leading producers of silicon metal, Elkem Solar has a centralised R&D environment with more than 150 scientists and technicians employed. The company has built strong relations with the electronics industry and has been working on the development of silicon for solar cells and electronics since the early 1980s.
Although the first solar-grade silicon line was discontinued due to the lack of sufficient demand from the market, the company did not stop its research and development in this area. And in 2006, after Orkla had taken over Elkem and incorporated it into its group, an investment project worth of NOK 2.7 billion (EUR 300 million) was launch to build the new solar silicon plant in Kristiansand.
Once the plant is commissioned later in 2009, Elkem Solar aims at producing 6,000 tons of solar-grade silicon a year. In solar cells, this amount of silicon is able to produce 650 MW of energy, or an electricity supply for a town of 55,000 for a year.
Solar energy is not the only industry that uses silicon, but it sets high standards for silicon purity. In order to achieve the necessary level of purity, the Elkem Solar plant uses new, patented technology based on Elkem’s long traditions in the field of silicon production.
The final product of the plant is a brick-size 10-kilo ingot made of purified silicon. Solar cell manufacturers then melt and crystallise into ingots. The ingots are cut into wafers and then add dopings and other enrichment to make them capable of converting sunlight into electric power and thereby becoming solar cells.
Innovative approach
Elkem’s final product contains a low amount of phosphor and boron, widely used in the industry for the purposes of controlling silicon’s electrical properties. An advantage of Elkem’s product is that it is ready to use. It does not need any additional doping.
Most competitors still use a gas deposition method for purifying silicon, which is an energy-consuming and costly process.
The metallurgical production process at Elkem Solar is a step up compared to major silicon producers in the world which use gas phase technology, a part that requires a lot of energy.
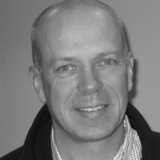
“The energy savings possible in our production process stem exactly from skipping this phase. This helps us save energy and costs.”
Helge Aasen
Senior Vice President, Business Unit, Elkem Solar.
Compared to its competitors using gas phase technology, Elkem consumes about one third of the energy. It also keeps its gas emissions to the air at the level of one third compared to other solar-grade silicon producers.
Elkem Solar’s furnace produces 600,000 cubic metres of waste gas an hour, but you see no smoke from Elkem’s chimney.
“There used to be a huge white cloud rushing up from the silicon furnace before we introduced a filtering technology that clean the hot gases,” Mr Aasen explains.
Elkem is now helping implement the same gas particle filtering in metallurgical plants in China.
Tiny share, optimistic outlook
It was a bold decision made back in 2006 to start up the industrial production of solar-grade silicon feedstock. Silicon may well have won the competition among materials for solar cell production. The solar energy share of total global electricity production is only 0.23%. Solar energy is and will continue for some time to be dependent on state subsidies to make it financially viable for consumers even in the sunniest parts of the world, such as Spain or California.
Yet, the solar market seems to be less affected by the global financial and economic crisis. Elkem Solar is confident and optimistic about the future. Its contract with German Q-Cells, the world’s largest solar cell producer, for half of Elkem Solar’s production is in force until 2018.
In its World Energy Outlook published in November 2008, the International Energy Agency (IEA) expects modern renewable technologies to become the second largest source of electricity soon after 2010, after coal. Falling costs, higher fossil fuel prices and strong policy support would help eliminate the renewable industry’s reliance on subsidies and bring emerging technologies into the mainstream.
The IEA expects solar, along with wind, geothermal, tide and wave energy, to grow faster than any other source worldwide, at an average of 7.2% annually. The share of non-hydro renewables in total power generation is expected to grow from 1% in 2006 to 4% in 2030.
Cost reduction a priority
“The competitiveness of solar energy depends on how soon we reach the so called grid parity, that is, when the solar energy price is at the same level as more conventional energy sources. All in all it comes down to the module installation cost and of course how many sun hours you have,” says Mr Aasen.
A country like Spain with its 1,800 sun hours a year will clearly reach grid parity much faster than a country like Norway with no more than 800 annual sun hours on average.
“It is a general belief in the industry that costs will be much lower within the next three to six years,” Mr Aasen adds.
Cost reduction is one of the priority areas for Elkem’s R&D. The target is to reduce the costs of electricity supplied to the consumer by at least 20% from the current level by 2010.
“This will only be possible on the basis of further development of industrial know-how. The industry is transforming itself from a craft industry producing small volumes, into a large-scale industry. If the costs are cut as planned, the solar industry will become competitive in large geographical areas”, Mr Aasen explains.
The industry is learning to get more and more out of silicon. The thickness of the silicon layer used for wafer production was 0.2 millimetres three years ago. Now it’s 0.16 millimetres.
Orkla and solar energy
With roots back to 1654 when it began as a mining company, Orkla has developed into a large international industrial group with stakes in a vast variety of business sectors, such as branded consumer goods, aluminium solutions, materials, renewable energy and financial investments. The group has a turnover of NOK 66 billion (EUR 7.5 billion) and 32,000 employees in more than 40 countries.
In recent years, when it gradually became clear that solar energy was developing into an attractive market, Orkla allocated a substantial amount of capital for further investment in this industry.
Since 2005, Orkla has two important interests in this industry: Elkem Solar and a stake in another important solar energy company in Norway, Renewable Energy Corporation ASA (REC).
“These companies were identified as having significant potential for value creation. It is a major investment in a high-growth industry. Together with Orkla’s stake in REC, the Elkem Solar plant represents a strategically important position in this industry,” says Geir Solli, Senior Vice President Finance at Orkla.
Speaking about the loan received from NIB for the Elkem Solar investment programme, Mr Solli adds:
“The new loan confirms NIB’s position as an important lender to our group. Orkla has enjoyed good relations with NIB for many years. Based on its financial strength and long-term perspective, NIB adds value as a reliable, attractive source of long-term financing.”